Liquid fertilizer production line
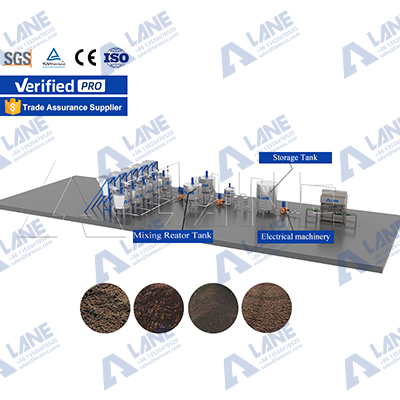
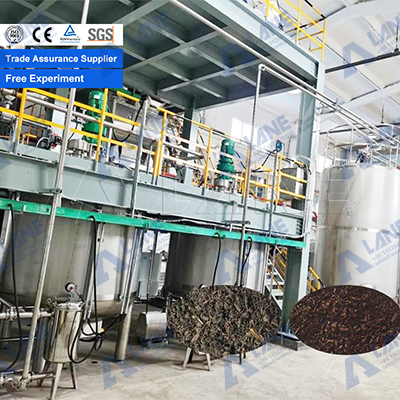
Liquid fertilizer production line is a combination of equipment used to produce liquid fertilizers, which usually includes a number of processes such as raw material treatment, mixing and reaction, filtration, storage and filling.
The raw materials used for chemical and organic liquid fertilizers are different because they have different preparation principles and target properties. The following are some of the raw materials that may be used in both:
Raw materials for chemical liquid fertilizer production line:
Urea (Nitrogen source): Urea is a common source of nitrogen and provides the nitrogen needed by plants.
Phosphates (phosphorus source): Diammonium phosphate, triammonium phosphate, etc., are used to provide plants with phosphorus.
Potassium Chloride, Potassium Sulphate (Potassium sources): Provides the plant with potassium.
Sulphuric acid, nitric acid, etc. (acid or alkaline regulators): used to adjust the acidity or alkalinity of liquid fertilizers to ensure a suitable pH value.
Trace element compounds: e.g. boric acid, zinc sulphate, etc., to provide the trace elements needed by plants.
Raw materials for organic liquid fertilizer production line:
Organic matter: including animal and plant manure, humus, seaweed, fermentation waste, etc., is the main raw material of organic liquid fertilizer.
Plant extracts: such as plant impregnation, plant extracts, etc., can provide organic liquid fertilizer with nutrients needed by plants.
Biomass charcoal (biochar): It can improve soil structure, increase water retention, and serve as a carbon source.
Microbial fungicide: Helps decompose organic matter and increase the biological activity of the soil.
It is important to note that organic liquid fertilizers often focus on providing a full range of nutrients through organic ingredients, while emphasizing the promotion of soil health and microbial activity. The ingredients in organic liquid fertilizers are more focused on natural, environmentally friendly and sustainable properties.
The raw material formulation of each liquid fertilizer product will be carefully blended according to crop demand, soil characteristics and production standards. Our products will be adjusted and increased or decreased according to the characteristics of the customer’s raw materials in order to meet the customer’s production needs.
Liquid fertilizer production line process:
1.Raw material processing stage:
a. Batching machine, pulverizer:
Some raw materials may need to be pre-treated, such as crushing and soaking of granular raw materials for better mixing and reaction.
2. Stirring and additive mixing stage:
a. Agitation tank:
Before mixing and reacting, use the agitator to mix the raw materials sufficiently to ensure that the raw materials are evenly mixed.
b. Additive mixing tank:
After agitation, the raw materials are fed into the additive mixing tank for mixing of additives. These additives may include acid-base regulators, surfactants, etc. to adjust the properties of the liquid fertilizer.
3. Mixing reaction stage:
a. Mixing Reactor:
The stirred and additive-mixed raw materials are fed into the mixing reactor for thorough mixing and chemical reaction. At this stage, reactions such as acid-base neutralization may occur to ensure uniform distribution of nutrients.
b. Macromolecular mixing reactor:
For organic liquid fertilizer, macromolecule mixing reaction may be required to process organic substances, etc.
4. Filtration stage:
a. Filters:
Use filters, such as duplex filters, to remove impurities and particles that may be present after the mixing reaction.
5. Storage phase:
Use filters, such as duplex filters, to remove impurities and particles that may be present after mixing and reaction. a. Storage tanks:
Store the mixed and filtered liquid fertilizer in storage tanks to provide a stable source for subsequent filling and packaging.
6. Filling Stage:f
The liquid fertilizer will be filled in the storage tank.
a. Automatic Filling Machine:
Automatic filling of liquid fertilizer to ensure accuracy and efficiency of packaging. Pack the liquid fertilizer according to the set specifications, which can be in different forms such as bottles and bags to meet the market demand.
Liquid fertilizer production line has multiple advantages, which cover production efficiency, product quality, market competitiveness and environmental friendliness. The ollowing are the main advantages of liquid fertilizer production line:
1. Efficient production:
Automated equipment and advanced production technology enable liquid fertilizer production line to achieve high production efficiency. The automation control system can increase the production speed, reduce the production cost and reduce the manual operation.
2. Stable product quality:
Advanced mixing reactor, filtration system and control system ensure the stable quality of liquid fertilizer, the product has consistent chemical properties and uniform particle size.
3. Flexibility and diversity:
The production line is designed with flexibility, which can adjust the formula and product specifications according to the market demand and customer requirements, and adapt to the needs of different plants and soils.
4. Space saving:
Liquid fertilizer production line compared to the production line of granular fertilizer, the machinery used usually covers a smaller area, suitable for production environments with space constraints.
5. Market competitiveness:
By providing high-quality, high-efficiency liquid fertilizer products, the production line can establish a competitive advantage in the market, and attract more customers through the plants face the advantages of liquid fertilizer easy to absorb fast.
We provide a full set of liquid fertilizer production line equipment as well as the project plan, according to the customer’s needs for experiments and formulations, to ensure the quality of the finished product, to provide a five-year warranty as well as after-sales service, you do not need to worry about any purchasing problems!